来源:折建刚 循环流化床发电
近年来,我国的新能源技术及其发电装机飞速发展。2020年风电、太阳能发电累计总装机达到5.34亿 kW,预计到2030年,其总装机容量将达到12 亿kW以上。由于新能源具有随机性、间歇性等特点,导致电网供电不稳定。为全面提高新能源消纳能力,我国提出了提升火电机组的灵活性运行能力,挖掘燃煤机组调峰潜力的要求。
循环流化床(CFB)发电技术具有炉内高效脱硫抑氮、燃料适应性广等优越性能,在我国得到了广泛应用。CFB机组由于其特有的灰循环系统可维持炉内较高的床温,蓄热量较大,保证了超低负荷稳燃,一般其最低稳燃负荷即可达30%,具有较强的深度调峰优势。CFB锅炉NO x 超低排放技术大多数选择“炉内燃烧优化调整+选择性非催化还原喷氨法(SNCR)”烟气脱硝的技术路线。但当CFB锅炉深度调峰运行时,CFB锅炉受其流化安全特性的影响,运行一次风量不低于临界流化风量,一次风量保持不变,炉膛出口过量空气系数通过调整二次风量来控制,造成锅炉炉膛密相区氧量过剩,同时二次风份额的减少导致锅炉分级燃烧效果不佳,导致NO x 原始排放生成。对于炉外NO x 脱硝技术,SNCR系统主要布置在分离器入口,脱硝还原剂主要采取尿素溶液,最佳反应温度区间为800~1 100 ℃。随着锅炉负荷的降低,锅炉炉膛运行床温及分离器入口温度也降低,当分离器内烟温低于800 ℃时,导致炉外脱硝效果降低。因此,CFB锅炉深度调峰期间,NO x 超低排放控制较为困难。
烟气再循环技术是一种在CFB锅炉低负荷运行中实现部分烟气替代一次风量的技术。通过早期工业炉应用效果显示,烟气再循环技术既能保证CFB锅炉安全流化风量需要,又能降低锅炉密相区氧量,增加密相区还原气氛,降低NO x 生成。同时烟气再循环技术还能使锅炉炉膛密相区燃烧推迟,使上部烟温升高,使分离器入口温度随之升高,可同步提高低负荷时SNCR脱硝效率,但该技术在大型CFB锅炉机组上的运行经验较少。因此,对已改造烟气再循环系统的某台300 MW亚临界CFB机组,对烟气再循环系统投、停前后进行热态试验,研究烟气再循环技术投停对锅炉燃烧、污染物排放等主要运行参数的影响,通过性能测试对比分析烟气再循环改造后运行效果及经济性,为大型CFB机组深度调峰时烟气再循环运行提供技术参考。
1 研究对象及方法
1.1 锅炉及环保设施
某台300MW亚临界CFB锅炉型号为HG-1065/17.5-L.MG44型,整体布置为裤衩腿型、双布风板单炉膛结构、H型布置。锅炉燃烧室断面呈长方形,宽×深×高分别为16.617 m×16.269 m×44.700 m,燃烧室下部分成裤衩腿形式,包括2 个风室和2 个布风板;炉膛内布置有屏式II级过热器管屏、末级再热器管屏、水冷蒸发屏;4 个分离器为内径约8 m的高温绝热分离器,每个分离器回料腿下布置1 个非机械型回料阀,回料为自平衡式。尾部烟道采取双烟道结构,前烟道中布置有低温再热器,后烟道中布置有高温过热器及低温过热器,上部烟道为膜式包墙过热器所包覆,下部为单烟道,自上而下依次布置有省煤器及空气预热器,省煤器采用H型省煤器顺列布置,空气预热器采用管式空气预热器。锅炉采用4 条给煤线分别把原煤送到回料阀的回料腿,锅炉左右侧各配置3 台滚筒式冷渣器,排渣温度不超过150 ℃,锅炉主要设计参数见表1。
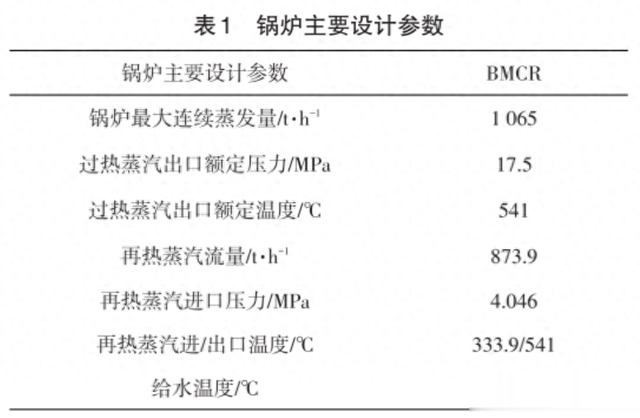
该锅炉污染物排放均执行超低排放标准。脱硫采用“炉内脱硫+炉外循环流化床半干法”工艺,脱硫剂分别采用石灰石粉和消石灰,烟囱出口SO 2 排放浓度小于35 mg/Nm 3 (基准含氧量6%,下同);其中炉内脱硫采用石灰石粉气力输送方式送至锅炉炉膛,左右侧回料腿各2个,内下二次风左右炉膛各2个,共8个石灰石加入点。NO x 超低排放采取“分级燃烧+SNCR系统脱硝”方式,SNCR选用尿素为还原剂,烟囱出口NO x排放浓度小于50 mg/Nm 3 。除尘采用“预电除尘器+脱硫布袋除尘器”方式,烟尘排放浓度小于10 mg/Nm 3 。其工艺流程具体如图1所示。经过超低排放工艺处理后的烟气在袋式除尘器出口温度控制在70 ℃。
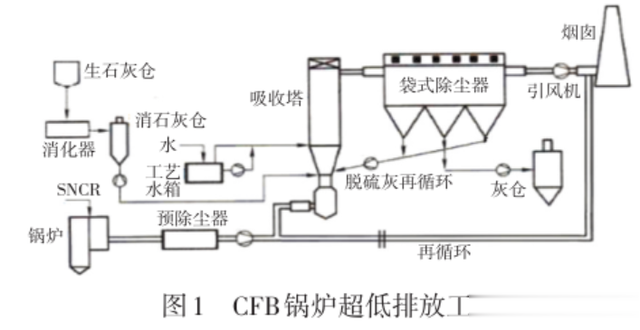
1.2 烟气再循环系统
烟气再循环系统流程如图2所示。改造主要包括:利用引风机出口压头,从引风机出口汇合烟道处抽取烟气,通过烟气主管道分成2 条支管路接入2 台烟气再循环风机,再经过风机出口配套支管路分别接入A、B一次风机进风口;烟气主管道至分叉支管路上进入烟气再循环风机前,各加装1 个电动调节门,经烟气再循环风机后的支管路上各加装1 个电动关断门,每个支管路进入一次风机前各加装1 个电动调节门,实现与尾部烟道和一次风系统的切断和隔离功能。锅炉各风机及烟气再循环风机主要设计参数见表2。

1.3 研发方法
为分析烟气再循环改造后运行效果,开展了CFB锅炉烟气再循环投运前后热态试验及相关性能测试,采集稳定工况下相关数据,分析研究烟气再循环投停 对锅炉燃烧工况、经济指标的影响。该锅炉长期运行负荷为 150 MW、300 MW,烟气再循环风量占一次风量比例最高为40%。因此,以下选取150 MW、300 MW负荷时烟气再循环风量占一次风量比例为40、0%工况研究,见表3,试验期间煤质及石灰石参数见表4~5。


锅炉炉膛运行床温、上部差压、分离器入口温度、排烟温度、空预器入口氧量、风机电流等运行参数,均来自稳定工况下同一时间段DCS系统数值,污染物排放浓度来自烟囱CEMS仪表数值(基准含氧量6%),底渣及飞灰可燃物含量、经济性指标来自按照性能试验要求进行试验的结果,仪器型号及精度见表6。

2 烟气再循环对锅炉燃烧影响对比分析
2.1 锅炉启动时NO x 排放的影响
如图3所示,锅炉热态启动过程中,SNCR系统未投运,一次风量244 kNm 3 /h,二次风量202 kNm 3 /h,NO x 瞬时排放值为原始排放值。锅炉负荷45 MW时,NO x 排放瞬时值为178 mg/Nm 3 ,烟气再循环风量83 kNm 3 /h,此时运行氧量为9.5%;期间保持锅炉负荷不变,随着烟气再循环风量进一步增加至195 kNm 3 /h,空预器入口氧量逐步降低至2.7%,NO x 排放逐步降低并稳定至26 mg/Nm 3 。
在锅炉启动过程中,烟气再循环的投入能明显控制空预器入口氧量至3.0%,从而在炉内密相区形成强还原气氛,明显抑制NO x 排放浓度的原始生成。因此,在锅炉启动或低负荷运行中,可根据锅炉运行氧量情况,及时投入烟气再循环,保证污染物环保达标排放。
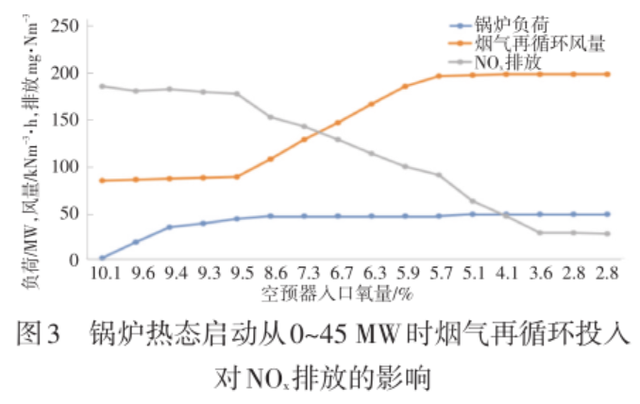
2.2 锅炉运行床温影响
对比烟气再循环投运前后相同负荷工况下床温变化,如图4所示。投运后锅炉炉膛下、中、上3 层床温均明显下降;300 MW稳定工况时,锅炉炉膛下部床温由投运前的897 ℃,降低至投运后的880 ℃,床温下降17 ℃;150 MW负荷时,锅炉炉膛下部床温845 ℃,相比投运前869 ℃,下降24 ℃。投入烟气再循环后,由于锅炉炉膛密相区氧气含量减少,造成炉膛密相区缺氧燃烧,导致锅炉运行床温下降。

2.3 锅炉上部差压的影响
CFB锅炉外循环物料量的增加对维持炉膛内燃烧均匀性和抑制污染物排放有较好效果,如图5所示。烟气再循环投入后,高、低负荷情况下,上部差压基本无明显变化,说明烟气再循环投入后,虽然锅炉总风量增加,但对上部差压影响较小。
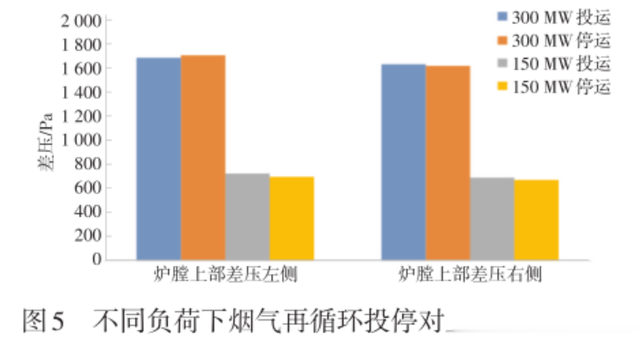
2.4 分离器入口温度的影响
分离器入、出口温度对SNCR脱硝系统的运行效率有着至关重要的作用。对比烟气再循环投运前后相同负荷工况下分离器入、出口烟温变化,如图6所示。投运烟气再循环后,300 MW负荷时分离器入口烟温整体降低5 ℃;150 MW负荷时,对比烟气再循环投入前,投运后分离器入口温度维持不变。但在300 MW和150 MW负荷下分离器入口温度在800 ℃以上,烟气再循环投停带来的分离器烟气温度变化很小,对SNCR脱硝效率无影响。
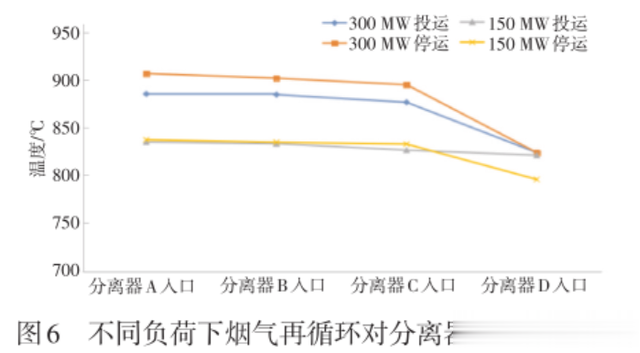
2.5 排烟温度的影响
由图7分析可知,300 MW负荷时,相比于投入前,投入烟气再循环后排烟温度升高3 ℃;150 MW负荷时,投入烟气再循环后升高12 ℃。投入烟气再循环后的排烟温度升高主要是受空预器漏风及其换热效率、锅炉燃烧工况的变化等因素造成。

2.6 污染物排放的影响
如图8所示,在锅炉稳定运行工况下,保持SNCR脱硝尿素溶液流量不变的情况下,烟气再循环投入前后,SO 2 、NO x 排放均能满足超低排放要求。

相比于未投入烟气再循环,在投入烟气再循环条件下,NO x 排放浓度的瞬时值和时均值降低;300 MW负荷时,投入烟气再循环后NO x 排放瞬时值降低13mg/Nm 3 ,小时均值降低6 mg/Nm 3 ;150 MW负荷时,投入烟气再循环后NO x 排放瞬时值降低6 mg/Nm 3 ,小时均值降低7 mg/Nm 3 。SO 2 排放受炉内脱硫因素及炉外脱硫系统的影响而变化不同。烟气再循环投入后,由于锅炉运行床温降低,且锅炉炉膛密相区处于缺氧燃烧,还原气氛增强,可有效抑制NO x 原始生成。
3 烟气再循环对运行经济性影响的对比分析
3.1 风机电耗的影响
如图9所示,相对比于未投烟气再循环情况,投入烟气再循环后,300 MW负荷时二次风机和引风机电流明显增加,锅炉风机总电流增加260 A,150 MW负荷下增加107 A。因烟气再循环投入,一部分烟气替代原有一次风量,在锅炉总一次风量基本不变的情况下,为保证锅炉燃烧所需氧量,锅炉二次风量增加;因烟气再循环投入,造成锅炉总烟气量增加,从而导致锅炉引风机电流增加明显。

3.2 底渣及飞灰可燃物含量的影响
如图10所示,相比于投入前,投入烟气再循环后,300 MW负荷下底渣、飞灰可燃物含量升高明显,底渣可燃物含量上涨1.2%,主要原因为锅炉密相区缺氧燃烧造成;飞灰可燃物含量上涨1.9%,主要原因为锅炉炉膛运行风量增加明显,导致飞灰未被分离器捕捉下来造成逃逸。
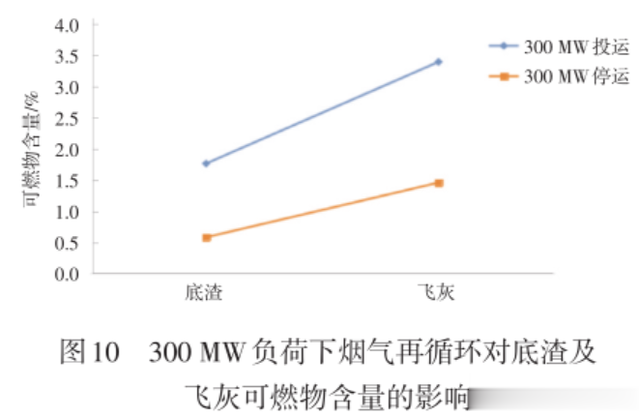
3.3 经济指标的影响
按照性能试验相关标准,测试300 MW负荷下烟气再循环对锅炉运行经济性的影响,具体见表7。试验结果表明:相对于未投烟气再循环情况,300 MW负荷投入烟气再循环后,在烟气再循环风量占一次风量比例为40%工况下,机组厂用电率由9.41%升高至10.26%,上涨 0.85%,锅炉效率由 92.47%降低至90.62%,锅炉效率下降1.85%,烟气再循环投入后导致锅炉运行经济性下降。
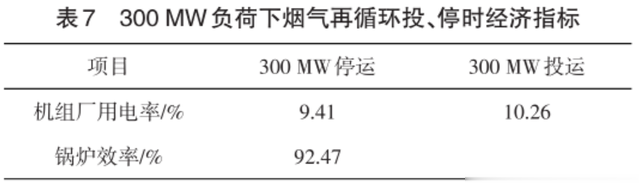
4 结 论
通过烟气再循环在锅炉启动及高、低负荷下热态试验对比分析得出:
(1)在锅炉启动过程中,投入烟气再循环能有效降低空预器入口氧量至3.0%,增强密相区还原气氛,从而抑制NO x 原始生成。
(2)锅炉正常运行中,投入烟气再循环后,300 MW和150 MW负荷下锅炉运行床温降低17 ℃和24 ℃,排烟温度上涨3℃和12℃,NO x 排放瞬时值降低13mg/Nm 3和6 mg/Nm 3 ;而上部差压及SO 2 排放变化不明显,分离器入口烟温变化不同,但在800 ℃以上,对SNCR脱硝效率无影响。
(3)在烟气再循环风量占一次风量比例为40%时,300 MW工况下,锅炉风机总电流增加260 A,底渣及飞灰可燃物含量分别增加1.2%和1.9%,厂用电率上涨0.85%,锅炉效率下降1.85%。因此,今后电厂机组高负荷运行时,可通过烟气再循环系统进行燃烧调整,降低锅炉运行床温;深度调峰时,需进一步优化烟气再循环系统的运行方式和循环风量,增强锅炉炉膛密相区还原气氛,利于深度调峰时环保排放达标。
文献信息
折建刚,谢国威,邬万竹.烟气再循环对循环流化床锅炉燃烧影响的对比研究[J].能源科技,2021,19(05):84-89.