摘要:本文深入探讨了锂电池涂布过程中出现暗痕的原因,并提出了相应的解决措施。通过对涂布过程中刀口状态、颗粒卡阻、涂布速度、加热条件等因素的分析,明确了暗痕产生的机制。同时,从确保涂布一致性、控制烘干过程、优化涂布工艺和加强质量检查等方面给出了具体的解决方法,旨在提高锂电池的质量和性能。
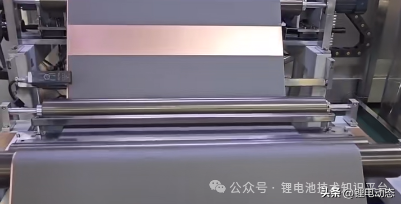
一、引言
锂电池作为一种重要的储能装置,其性能和质量受到广泛关注。在锂电池的生产过程中,涂布是关键工序之一,而涂布暗痕的出现会严重影响电池的性能和一致性。因此,深入研究锂电池涂布暗痕的原因及解决措施具有重要的实际意义。
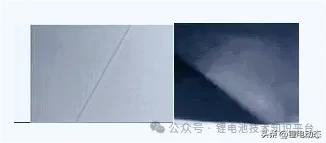
二、锂电池涂布暗痕产生的原因
(一)刀口问题
1. 刀口有异物
在拉浆过程中,若刀口处存在异物,如灰尘、杂质等,会阻碍浆料的均匀涂覆,导致极片表面局部厚度异常,从而产生暗痕。
2. 刀口表面不平整
刀口表面的不平整会使浆料在通过时受到不均匀的压力,造成极片表面厚度不一致,出现暗痕。
(二)颗粒卡阻
1. 辊压前颗粒卡阻
在辊压前,未打开的颗粒或小的干浆料可能会卡在刀口上,随着涂布的进行,在极片表面形成线状痕迹,表现为暗痕。
2. 辊压后颗粒卡阻
辊压过程可能会使原本隐藏的颗粒问题暴露出来,卡在刀口处,导致后续涂布产生暗痕。
(三)涂布速度不稳定
涂布速度对浆料在集流体上的涂覆效果有着显著影响。速度过快时,浆料来不及均匀铺展,易出现局部堆积或厚度不均;速度过慢时,浆料可能会过度干燥,导致表面粗糙度增加,两者都可能引发暗痕。
(四)加热条件不当
1. 加热温度不足
加热温度不足会导致浆料中的溶剂去除不充分,粘结剂结晶不完全,影响极片的结构和性能,容易产生暗痕和活性物质脱皮等问题。
2. 加热温度过高
过高的加热温度可能会使粘结剂过度结晶,破坏浆料的微观结构,同样会导致暗痕和其他质量问题。
三、解决锂电池涂布暗痕的措施
(一)确保涂布一致性
1. 监测浆料粘度
浆料粘度的变化会直接影响涂布的效果。应定期检测浆料的粘度,确保其在合适的范围内。当粘度发生较大变化时,及时调整配方或工艺参数。
2. 控制料斗液位高度
稳定的料斗液位高度有助于保持涂布压力的恒定。通过液位传感器和自动控制系统,实时监测和调整料斗内的浆料量,避免液位波动对涂布质量的影响。
3. 稳定涂布速度
采用高精度的调速装置和闭环控制系统,确保涂布速度的稳定性。在生产过程中,根据不同的浆料特性和涂布要求,优化设定涂布速度,并对速度波动进行实时监测和补偿。
(二)控制烘干过程
1. 合理设置烘干温度
根据浆料的组成和特性,通过实验和模拟确定最佳的烘干温度曲线。在保证溶剂充分去除的前提下,避免温度过高对粘结剂和活性物质造成损害。
2. 优化烘干时间
过长或过短的烘干时间都会影响极片的质量。通过热分析和实际生产测试,确定合适的烘干时间,以确保粘结剂结晶充分,同时防止过度干燥。
(三)优化涂布工艺
1. 改进涂布机设计
对涂布机的刀口结构、涂布头的形状和尺寸等进行优化设计,提高涂布的均匀性和精度。采用先进的流体模拟技术,对浆料在涂布过程中的流动行为进行仿真分析,为涂布机的设计改进提供理论依据。
2. 采用先进涂布技术
如狭缝涂布、喷雾涂布等先进技术,能够更好地控制涂布厚度和均匀性,减少暗痕的出现。同时,不断探索和引入新的涂布材料和工艺,提高涂布质量和效率。
(四)加强质量检查
1. 涂布和烘干前的检查
在涂布和烘干前,进行三次严格的检查。包括对极片厚度的测量,使用高精度的测厚仪,多点测量,确保厚度均匀;对浆料质量的检测,观察有无颗粒团聚、沉淀等现象;对极片尺寸的检查,保证尺寸符合设计要求。
2. 定期检查关键参数
定期检查制浆速度、烘烤时间和间隙等关键参数,与设定值进行对比,及时发现偏差并进行调整。建立完善的质量数据库,对检查数据进行记录和分析,为质量改进提供数据支持。
四、结论
锂电池涂布暗痕是一个复杂的问题,涉及到多个工艺环节和因素。通过对暗痕产生原因的深入分析,采取针对性的解决措施,如确保涂布一致性、控制烘干过程、优化涂布工艺和加强质量检查等,可以有效地减少暗痕的出现,提高锂电池的质量和性能。在实际生产中,需要不断总结经验,持续改进工艺和设备,以适应不断提高的锂电池质量要求。
文章来源:锂电池技术知识平台
注:本站转载的文章大部分收集于互联网,文章版权归原作者及原出处所有。文中观点仅供分享交流,不代表本站立场以及对其内容负责,如涉及版权等问题,请您告知,我将及时处理。