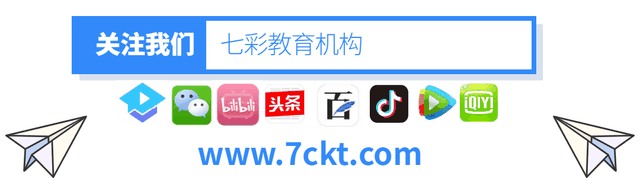
风电、光伏、水电以及传统的火电行业,都存在因弃光、弃风、弃水以及发电谷峰与用电谷峰不匹配带来的能源浪费问题[1-3]。据2016年的统计数据,全国因弃风、弃光而浪费的电能大约1000亿kW·h,价值数百亿人民币。以锂电池为代表的大规模储能系统是解决这一问题的有效手段,这对电池的可靠性和使用寿命提出更高的要求[4-6]。电池寿命受批量电池一致性、发热特性的影响显著,而电池一致性和热特性又受参数设计、结构设计、加工工艺、使用环境、成组技术和热管理方案等因素的影响。合适的电池单体成组技术和热管理技术,可改善电池的一致性和发热性能[7]。
采用电池储能系统既可以保证上网电压的稳定,又可以补偿有功功率,不会对系统产生不利的影响。储能电池体系主要有钠硫电池、液流电池、锂电池、超级电容器、铅酸电池以及飞轮储能、蓄水储能和压缩空气储能等[8-10]。锂电池凭借其较高的能量效率、较长的循环寿命、合适的响应时间以及较成熟的规模化市场,在电力调频中展示了很好的应用前景。目前,锂蓄电池已朝着大功率、高比能量和高循环寿命方向迅速发展,大型锂电池模块已经作为储能电池进入了电力储能系统[11-12]。
为开发满足国际技术要求兆瓦级储能系统,本文以26650电池为研究对象,针对100kW·h/480V储能电池子系统进行模块化结构设计、数值模拟和试验研究。根据储能系统对电池子系统模块温度一致性、电压电流一致性、机械可靠性、装配工艺性以及模块标准化要求,运用CFD流体传热计算机数值仿真模拟和实验方法对电池模块、集流板以及电池机柜的关键参数进行分析研究。研究表明:合理的电池间隙不仅让冷却风与每个电池进行充分热交换,还能改善风冷通道、减少模块体积;增加斜板设计可以使模块内部各电池组冷却均匀,有效解决电池因热累积带来的温升过高问题;集流板优化设计可以改善电池单体外连接件电阻的一致性,从而改善充放电电流和电压的一致性。
01
电池选型和模块集成
电池选型
大规模储能系统不仅对电池数量的需求量非常大,还要求批量电池具有非常严格的一致性。根据对各类电池(圆柱电池、软包电池和方形电池等)设计条件、制造工艺和质量控制等技术水准的调研,本文选用工艺成熟稳定、成品率高、可靠性高、一致性好、成本低、循环寿命长和传热面积大的磷酸铁锂体系26650圆柱电池,如图1所示,电池性能参数如表1所示。
该电池机械可靠性高、装配工艺灵活、运输安全,样品如图1(a)所示。金属壳体导热效果好,有利于热均衡设计;为防止电池短路,保证电池的安全性,电池两端易短路区均被套管覆盖;热塑橡皮套管内径26mm,外径为27mm。电池模型如图1(b)所示。
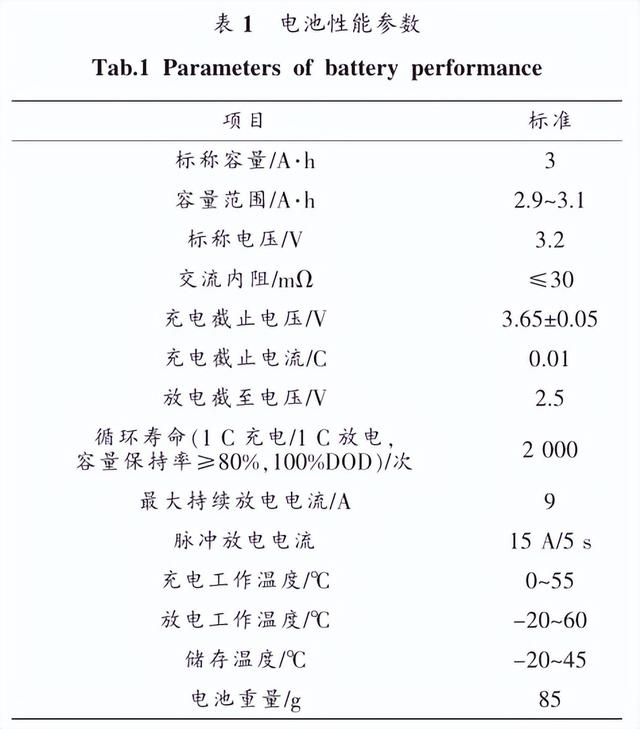
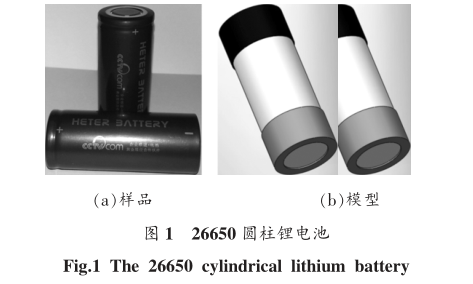
模块集成
电池模块由盖板、集流板和镍片等主要部件组合而成。盖板采用厚度2mm、槽深9mm的绝缘塑料材料,槽中有固定电池的小圆柱,如图2(a)所示。通过调整圆柱间距可以控制电池单体之间的距离。为节省空间,电池成组采用交叉排列,中间散热区域形成等距强迫对流风道,为下文不同间距成组方式散热能力的研究提供基础。
为了便于焊接,还需在盖板安装电池的位置处开孔,空径一般12mm左右。图2(b)为模块镍片、铜板连接关系,每列电池用一根厚度0.1mm的镍片连接,镍片安装在电池与集流板之间。为了便于极耳和数据采集线的安装,电池两端的镍片长度不相等。
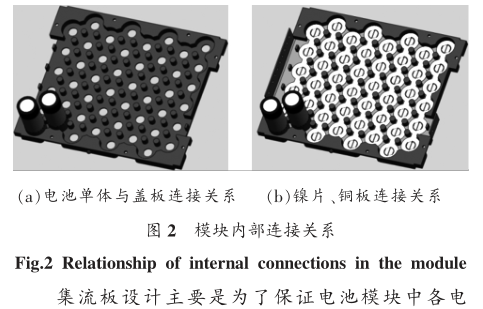
集流板设计主要是为了保证电池模块中各电池单体的外连接电阻的一致性,且与电池单体的连接稳固;为减少电流通过集流板产生的焦耳热,还要保证较小的欧姆电阻,如图3所示,图3(a)为集流板的双侧开耳设计方案,而图3(b)为集流板的单侧开耳设计方案。
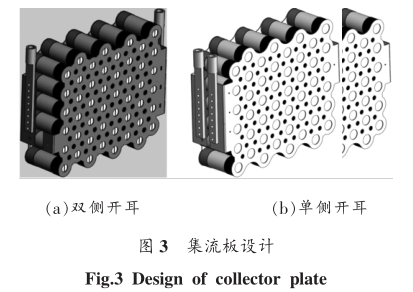
电池模块左右对称,组成模块时,只需一侧安装检测电压的连接线以及电连接器。极耳两侧安装极耳罩,盖板开孔安装螺栓,保证电池组的紧固。电池组由底部进风强迫冷却。上部出风散热。极耳处安装电连接片。极柱顶部设计成的沉孔,通过插入螺钉的方式,方便电池组之间的电连接。在集流板两侧分别安装极柱,极柱与集流铜板通过螺钉多点相连,极柱位置靠近每一侧的盖板。电池模块按照6×8交叉排列方式共48个电池并联组成,如图4所示。
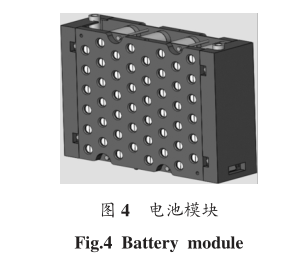
02
实验设备和设计
实验设备
电池模块发热测试是在实验室条件下进行的,动力电池充放电设备的主机和巡检仪如图5所示,还有与之配套的测试软件。测试设备为湖北德普电气股份有限公司生产的德普100V/150A4通道,型号BTS2000。为验证模拟方案的正确性,对该方案进行了初步实验验证,测试现场如图6所示。将
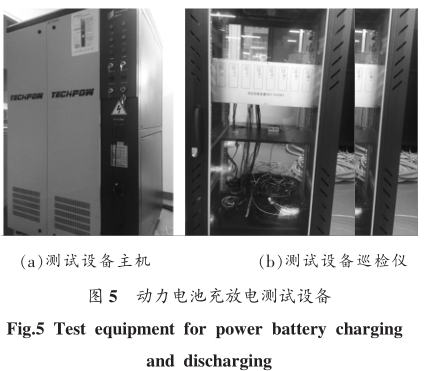
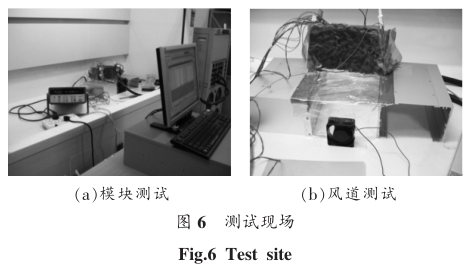
电池两端贴上胶带使电池中段保持有间距,用镍板将24个单电池并联起来,电池壳上分别贴上温度传感器,用风扇对电池组进行冷却,并在不同倍率下进行充放电实验。
实验设计
为研究电池单体间距对模块散热特性的影响,本文对6×8模块电池单体间距为1mm、2mm、3mm、4mm、5mm、6mm、7mm时模块温度分布分别进行实验测试,并对间距为2mm、4mm、6mm的模块进行仿真计算。实验测试和仿真的工况设置保持严格的一致,工况设置如表2所示。为研究充放电倍率对模块散热特性的影响,分别对充放电倍率为1C、2C时的模块进行实验测试,实验测试工况设置如表3所示

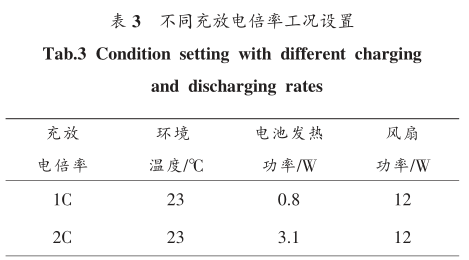
为研究集流板对模块散热特性的影响,本文设计集流板的结构参数为:集流板长、宽、厚为a、b、h,a=23.4cm,b=16.5cm,h=0.1cm,材料为黄铜。假定电堆在均匀的电流密度i(A·cm-2)下工作,对于高度为dx的微元集流板,微元的发热功率可表示为

式中,ρ为集流板的电阻率。式(1)积分可得到整个集流板在工作时候的发热功率为

根据式(1)、式(2)和环境温度工况,运用Excel软件进行编程计算。
为研究风扇风量对模块散热特性的影响,风扇的出风量与风扇功率有密切关系,本文对风扇功率为0、2、4、8和12W下的模块温度分别进行实验测试。当功率为0W时,可以认为电池模块采用的自然冷却方式,实验测试工况设置如表2所示;当风扇功率为12W时,电池间距为4mm时,利用风量仪测得风量为487L/min,充放电倍率均为1C,环境温度均为23℃,电池单体之间的距离均为4mm。
03
结果与分析
电池间距对模块温度分布的影响
图7为不同电池模块间距时电池模块温度场分布情况。当间距为2mm时,电池温度最高为32.6℃,最大温差11.6℃;随着间距增大,最高温度和温差都会有显著降低;虽然更大的间距,电池组温度会更低,但效果有限,且会大大增加模块尺寸。
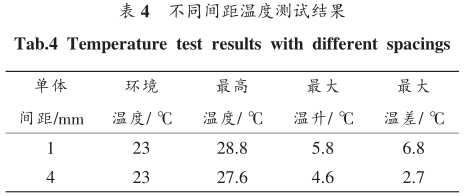
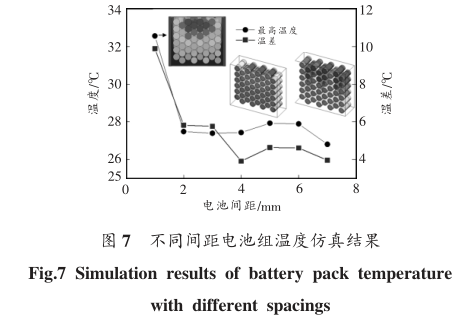
本文模块间距选用4mm,表4为工况测试数据。电池间距为4mm时,电池模块最高温度和模块温差最低。继续增大电池间距,对降低电池模块最高温度的能力开始下降,电池模块的温差也开始增大。直到电池间距增大为7mm时,电池模块的散热状态勉强接近间距4mm时的电池模块。因此对于本文研究的电池模块,电池间距选择4mm的设计参数可以让模块的散热状态达到较优的状态。
充放电倍率对模块温度分布的影响
表5为不同充放电倍率温度测试结果,1C充放电时电池最大温升为4.6℃,最大温差2.6℃。而2C充放电时电池最大温升为7.2℃,最大温差6℃。对于大规模储能系统,采用电池单体内部多并联接方式降低充放电倍率,可以降低电池的充放电倍率,从而不仅可以提高电池的使用容量和电压,还能提高电池的循环寿命。
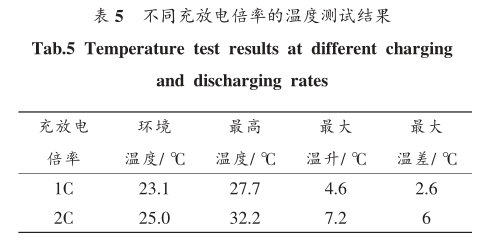
集流板设计对热电一致性的影响
如图8为集流板的厚度、长度对其发热功率的影响,集流板长度小于30cm时,其发热功率差异性较小;而厚度对发热则有成倍的影响。为了减少集流板的发热率选用0.2mm厚较好。根据公式编程计算可知,当集流板一侧开耳,靠近极耳处的电
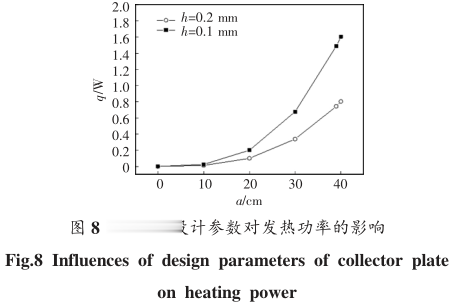
池与远离极耳处的电池焦耳热相差1.6W,这会使电池易失去一致性,导致热失衡。集流板采用两侧开耳的设计方案,可以提高电池单体外连接电阻一致性,从而保证充放电过程中的电流、电压和发热的一致性。
风扇风量对模块散热特性的影响
为探究冷却方式对模块温度分布的影响,通过控制风扇风量来模拟各种冷却工况下的散热情况。当风扇输入功率为0W时,电池模块采用的是自然散热方式;当风扇输入功率为全负荷12W时,电池模块采用的是强制对流散热。风扇功率为0、2、4、8和12W时,对应的风量分别为0、82、165、323和487L/min。
表6为风扇在不同功率下的温度测试结果,随着风扇功率的加大,最高温度和最大温差都显著降低。当风扇功率超过4W,进一步增大风扇功率对改善电池散热影响有限。在储能系统热设计中,对风扇风量的优化选型不仅可以获得较好的散热效果,还能降低系统能耗。一味地增大风扇功率,对进一步改善电池散热效果影响有限,还会增大风扇的系统能耗。对于本文研究的电池模块,采用功率4W、风量165L/min的风扇,既能满足模块的散热要求,又能节约系统的电功耗。
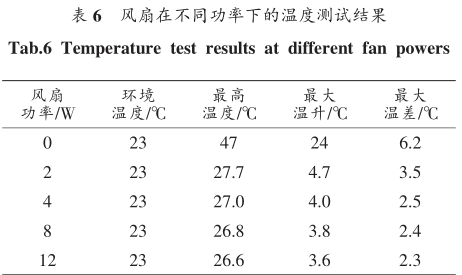
04
结论
(1)对于大规模储能系统,为了满足系统温差不超过5℃的技术要求,模组的充放电倍率最好不超过1C。采用电池单体内部多并联接方式增大容量,可以达到降低电池的充放电倍率的目的。低倍率、大容量的模组设计不仅可以提高电池的使用容量和电压,还能提高电池的循环寿命。
(2)通过模拟与实验相结合的方法设计电池间隙,使冷却风能有效接触每个电池进行热交换,提高换热效率。对于本文研究的电池模块,电池间距选择4mm时设计参数可以使模块的散热状态达到较优的状态。集流板长度超过300mm、厚度小于0.1mm时发热较为明显。板集流板双侧出耳的设计不仅能改善铜板发热的一致性,还能提高电池单体外连接件电阻的一致性。
(3)在储能系统热设计中,对风扇风量的优化选型不仅可以获得较好的散热效果,还能降低系统能耗。一味增大风扇功率,对进一步改善电池散热效果影响有限,还会增大风扇系统能耗。对于本文研究的电池模块,采用功率4W、风量165L/min的风扇,既能满足模块的散热要求,又能节约系统的电功耗。
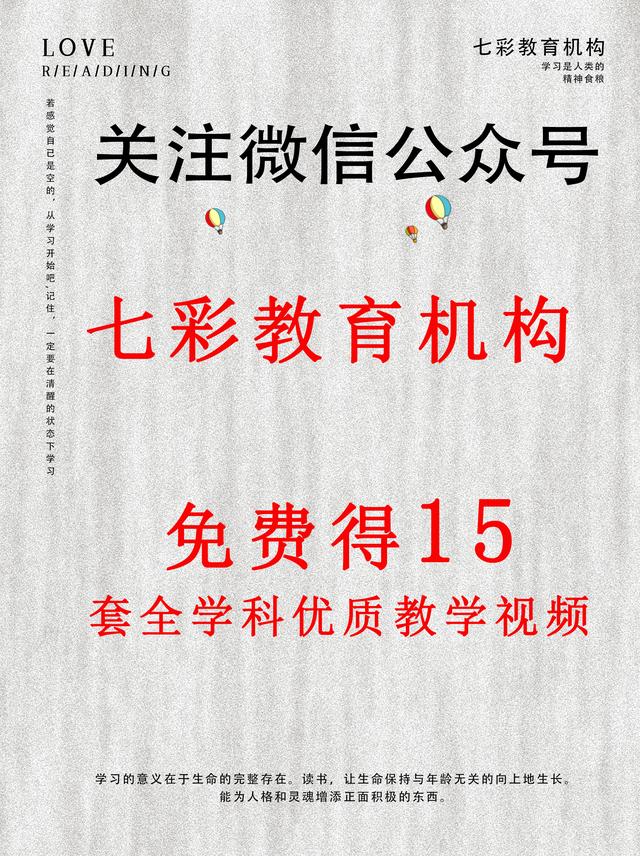