使用LFP正极 (徳方, DY-1) 通过双行星搅拌机制作浆料。因为第一次制作浆料时粘度太低第二天又追加制作。单面面密度12mg/cm2。在铝箔 (12μm) 上双面涂布。之后进行碾压,体积密度调整到2.3g/㏄。分切后,和负极一起进行折叠。正极的电极状态不是很好 (详细后面叙述) 。需要改善。
关于石墨负极 (中钢碳素化学, MG11),加入CMC、SBR,使用双行星搅拌机制作水系浆料。单面面密度5.6mg/cm2,在铜箔上双面电极涂布。之后进行碾压,体积密度调整到1.5g/㏄。分切后,和正极一起折叠。关于负极没有发现问题。
操作流程1.浆料制作工程
浆料的制作是在双行星搅拌机中进行搅拌的。
正极: LFP (徳方, DY-1): 93.3%, Binder S5130 (Solef): 2.5%, CNT (徳方, CN-1N分散液): 1.2%, SP (IMERYS): 3%
粘着剂在NMP中进行分散混合后,加入CNT溶液、SP进行分散。
添加LFP,真空去除气体后进行分散混合(刚开始以固含量50%进行调整)。然后边加NMP边确认调整粘度。
第一次 : 固含量43%3个小时,分散混合。
因为粘度太低,导致固含量下降过低。
第二次 : 固含量45%3个小时,分散混合。
粘度、规格范围 没有问题。
负极: 石墨 (中钢碳素化学, MG11): 94.5%, SBR (TRINSEO, Voltabond029): 1.5%, CMC (日本制纸, MAC500LC): 1.0%, SP (IMERYS): 3%
SBR, CMC添加到离子水中进行分散混合后,加入SP、石墨进行分散。固含量调整为50%。真空除气后,3个小时,分散混合。
粘度、规格范围,没有问题。
2.涂布工程
Gravure Coating Machine (3m/min.) 设备上进行。
正极
在12μm 铝箔上进行涂布。目标面密度: 12mg/cm2 (双面: 24mg/cm2)
干燥温度90℃ (有风)、干燥时间内4min. (一般)。
第一次和第二次的干燥时间都是4分钟,NMP完全没有蒸发干净。建议干燥时间追加2分钟。
负极
在8μm 铜箔上涂布,目标面密度: 5.6mg/cm2 (双面: 11.2mg/cm2) 。
干燥温度70℃ (有风),干燥时间4min. (一般)。
没有发现特别大的问题,完成涂布。
3.碾压工程
使用NAKNOR (LDHY400-N45) 碾压机 (常温碾压)进行碾压。
正极
目标体积密度:2.3g/㏄。
第一次 : 2.2g/㏄ (厚度:118-120μm) 。
第二次 : 2.3g/㏄ (厚度:117-118μm) 。
第一次和第二次做出的电极是脏的 (Fig.1)。
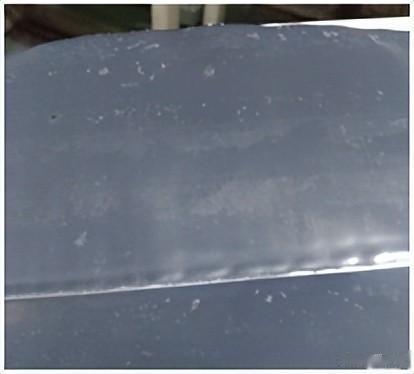
正极碾压后的电极表面
估计NMP没有完全蒸发干净是主要原因。
还有,在第二次 (1/11)电极碾压后,涂布尾部发生褶皱。涂布尾部的褶皱是因为涂布时,电极向上鼓起。如果铝箔一部分不使用的话,可以切掉涂布端的尾部来解决。但是这次制作的电池结构是需要铝箔的那部分的。所以今后,需要讨论如何预防涂布尾部的翘起或者直接更换铝箔的材质。
负极
目标体积密度:1.5g/㏄。
碾压2次后的体积密度: 1.5g/㏄ (83-85μm) 。
碾压1次的话,无法满足要求,所以碾压2次进行对应。碾压后的电极状态良好。对方没有确认剥离状况等。
4.分切~折叠~电极干燥工程
正极
切成111㎜×110㎜ (Tab: 35mm (宽度) ×20㎜ (高度))。
切割的边缘附近多多少少有些浮起,还能看到有些剥离的地方。
是切割电极的设备品质不好。电极的剥离强度也许存在问题。 (可能因为NMP没有蒸发干净,剥离状况变差) 。
负极
切割成114㎜×113㎜ (Tab: 35mm (宽度) ×20㎜ (高度))
分切时对方未确认电极翘曲状况和剥离状况。
将电极和16μm的PE隔膜进行折叠。
正极20片、负极21片。高度5.1㎜ (相当于额定8.2Ah) 。
折叠后发现Hi-Pot不良。
估计正极的电极翘曲和剥离变差是主要原因。
于是用刷子刷电极刷掉剥离物后,再进行折叠。
折叠好后在105℃进行真空干燥 (12h),在露点-40℃以下的干燥室内进行注液。
总结今后要改善的重点浆料制作过程
1.基本上,使用双行星搅拌机制作浆料的操作顺序,日本和韩国是不一样的。
关于浆料制作,作业员的等级是一个外行。关于正极粘着剂,并不是在行星搅拌机内直接混合,最好是要提前使用润湿分散剂进行溶解后再添加。因为使用行星搅拌机制作浆料不易充分分散,所以最好是提高固含量的情况下添加正极,固含量在80%左右的状态下进行固炼比较好。进行固炼时,因为粘度容易下降,所以稍微提高固含量,之后进行涂布时,干燥状态会变好。2.关于负极浆料制作也是一样。
一般是不会将CMC、SBR一起混合的。负极也是,添加SBR之前,先固炼会比较好。这次虽然没有发现负极的不良现象,但是如果稍微涂厚一点的话,估计问题就会出现。涂布工程3. 这次正极的干燥温度设定的是90℃,稍微再提高一些温度也是可以的。在生产中,为了加快干燥速度,有的提高到120℃左右。虽然说提高干燥温度,会出现粘着剂的Migration等问题,但是像这次的面密度来看,推测基本上不会有影响。
碾压工程
4. 这次碾压后的正极状态很差,如前述,通过改变浆料的制作条件,涂布时的干燥温度来可以得到改善。
5. 碾压机的滚轮上面有划痕,状态不好。碾压机的滚轮上面的划痕和翘曲带给电极的影响不能忽视,如果条件允许有必要对滚轮进行研磨。
分切∼折叠∼电极干燥工程
6. 为了抑制正极的电极剥离,分切时使用的刀具,需要更换新的,或者对刀具进行研磨,或者使用介质等隔绝开来。
关于以上这些,浆料制作时分散不彻底或者NMP残留等,都会导致剥离强度下降,所以通过改善这些,就有可能改善电极的剥离强度。