来源:张强 循环流化床发电
随着国内制造业朝着大型化、专业化、规模化的转型,众多企业和工业园区为满足自身能源需求新建动力站和自备电厂。这些动力站和自备电厂在提供电、热能源的同时,还往往担负着处置企业废弃物的任务。因此循环流化床(CFB)锅炉以其优良的燃料适应性受到广大用户的青睐。目前国内循环流化床在掺烧可燃废气方面,考虑到机组安全性、燃烧稳定性等问题一般掺烧比例不超过30%。但随着工业体系、工艺流程的调整,部分产业产生的废气已远超过这个比例。如能通过循环流化床设备实现更大比例掺烧可燃废气,一方面可彻底解决废气处理问题,消弭了通过其他处理方式对环境的影响;另一方面掺烧可燃废气节约燃煤,还能带来可观的收益,实现环境效益和经济效益双赢。
文中针对某220t/h有大比例掺烧低热值废气需求的CFB锅炉项目,对其进行了技术可行性分析。
1 项目基本情况
目前国内220t/h级CFB机组参数常规为高温高压和高温超高压,研究表明,目前在运行的此等级小火电机组因锅炉效率低、汽机热耗大、厂用电率高等原因,整机煤耗超过《常规燃煤发电机组单位产品能源消耗限额》
(GB21258—2013)。为获得更高机组效率,本项目将参数提高到超高温亚临界。锅炉蒸汽参数如表1所示。
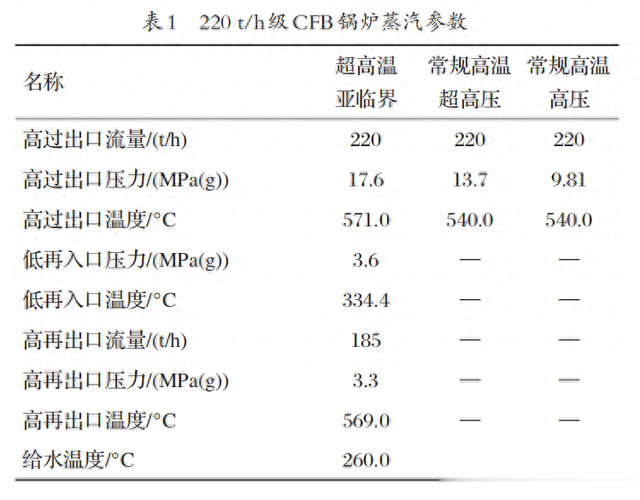
本项目设计煤质为矸石,灰分较高,热值偏低;设计掺烧废气为兰炭尾气,其中存在大量不可燃气体,综合可燃成分仅占44.9%,热值极低。根据具体项目情况,锅炉设计需考虑尾气掺烧范围为0~90%,常规掺烧比60%~70%。燃料情况如表2所示。
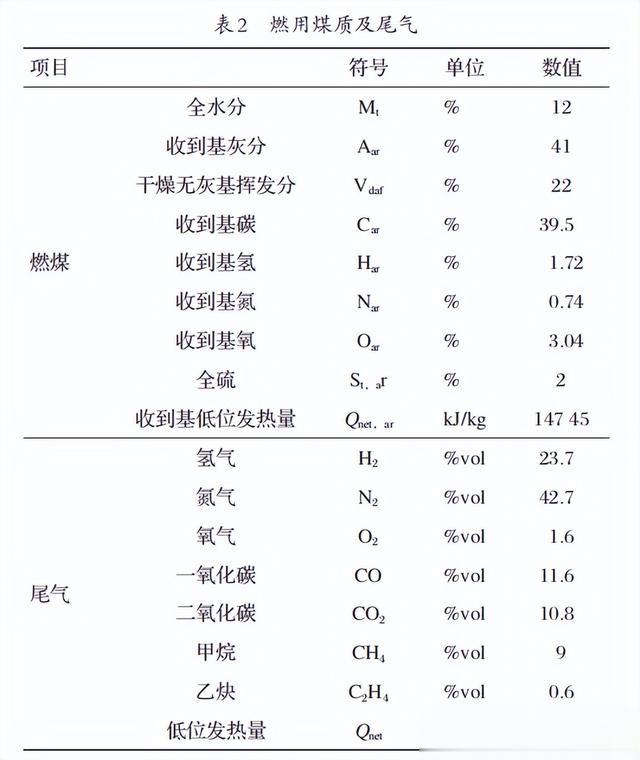
2 设计重点及关键技术
本项目220t/h级大比例掺烧废气CFB锅炉采用超高压亚临界带再热参数,锅侧设计需考虑过热受热面布置、水动力安全性、汽水阻力控制等,进行针对匹配设计;炉侧则需考虑通过何种方式实现稳定高效的大比例掺烧废气。其中锅侧相对成熟,因此炉侧设计为本方案设计的重点和关键。
由于废气燃烧特性与燃煤有较大差异,根据已运行项目经验,采用常规简单掺烧方式,掺烧比例超过30%就会对燃烧稳定性、锅炉负荷和效率有较大影响。而本项目废气掺烧比为0~90%,最大值远超过30%。因此常规掺烧方式并不适用,本项目设计需重点考虑如何在循环流化床设备中同时实现稳定的煤、气混合燃烧;在大比例掺烧时锅炉达到设计负荷;以及在满足前两者条件的基础上尽量提高锅炉效率。
2.1 煤、气混烧技术
煤与气体的燃烧不同,前者属于多相燃烧,后者属于单相燃烧。煤的燃烧发生在相界表面,从干燥、干馏到挥发分和焦炭的燃尽需要经历一系列复杂过程;气体燃烧则根据燃烧方式的不同,仅受限于扩散速度或化学反应速度。相比煤,气体燃料与氧气更易结合,当两种燃料同时在循环流化床内燃烧,易发生气体燃料抢夺煤燃料所需氧气的现象,可能造成煤燃烧不充分的问题。此外,一方面掺烧燃气挤压了燃煤的输入热量,减少了燃煤投入,降低了入炉固体物料量的主要来源;另一方面燃气配风取自给燃煤配风的一、二次风系统,减少了燃煤配风比例。一旦掺烧比例过大则可能因物料浓度低、流化风量小造成物料平衡破坏、流化状态等问题。
废气燃烧本身也存在很多问题:废气中存在大量不参与反应的N2与CO2,热值被大幅拉低,着火温度上升、火焰扩散速度减慢、采用常规燃烧方式可能出现脱火现象,引发燃烧稳定性问题;同时因废气燃烧集中,火焰温度高,NOx排放控制也是难点。因此循环流化床锅炉实现大比例的煤、气混烧,关键是避免煤、气燃烧相互干扰,提高煤、气燃烧稳定性,降低污染物排放。
本项目针对兰炭尾气进行了分析并设计了新型燃烧器。该燃烧器采用一、二次风门调节挡板、延迟混合环、二次风延迟混合板、一次风宽尺寸稳燃器等设计,保证兰炭尾气稳定燃烧的同时,NOx排放较常规燃烧器降低60%以上;考虑到炉内空气过量的环境,燃烧器配风采用了低过量空气系数设计,进一步降低原始NOx排放的同时还降低兰炭尾气燃烧对风量需求,将更多风量留给一、二次风系统,保障燃煤流化和燃尽。新型燃烧器示意图如图1所示。
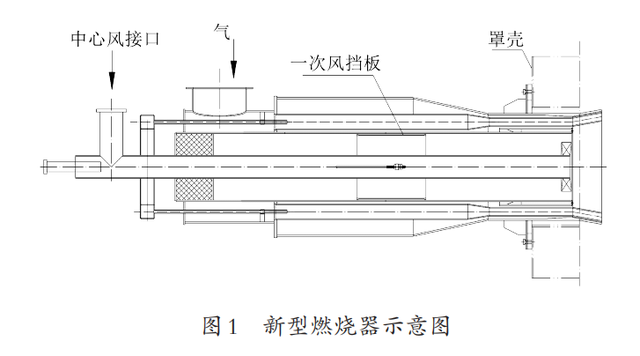
考虑到不同掺烧比的需求,以及避免火焰喷涂炉膛内壁的可能,燃烧器采用了侧墙分层分级布置,具体兰炭尾气燃烧器布置图如图2所示。
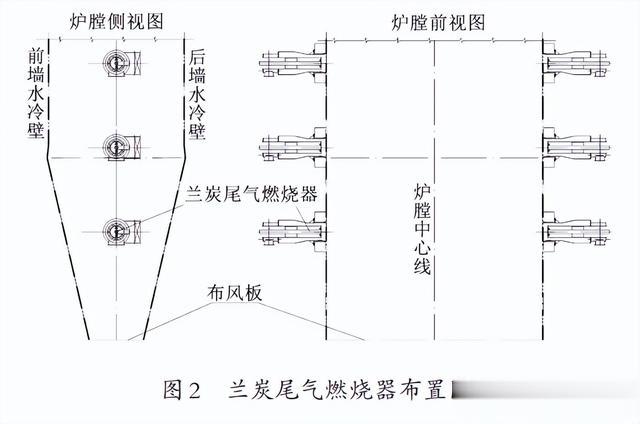
由图2可知,这种布置方式能够根据掺烧比例的不同,调整燃气投入位置和数量。低掺烧比例时投入中上层燃烧器,通过拉大兰炭尾气与炉底的距离,降低掺烧兰炭尾气对燃煤的干扰;高掺烧比例时,关闭燃煤二次风管,仅通炉底一次风保证流化状态,投入低层尾气燃烧器,尾气燃烧器代替部分二次风的作用,增强物料扰动,提高炉内煤气混合的均匀性,并借助尾气火焰局部高温的特点,提高密相区温度,促进煤的燃尽;当掺烧比超过70%,通过添加床料,可维持物料循环。
2.2 宽掺烧比达出力设计
虽然循环流化床锅炉具有宽燃料适应性的特点,但实际工程中常出现因燃料变化过大,锅炉难以达到设计负荷的情况,这种情况在掺烧低质废气时同样可能出现。因废气中有大量不参与反应的气体,同样输入热量时燃烧废气生成的烟气量大,平均烟温低,拉低了床温整体水平,进而影响炉内辐射传热能力,导致同样数量受热面的换热量降低。当掺烧比相对稳定时,新建机组可以通过增加炉内受热面解决出力不足问题,但当掺烧比不稳定、掺烧比变化较大时,则依旧可能出现更高掺烧比时出力不足,而低掺烧比时甚至会出现受热面超温现象。
为增强锅炉废气宽掺烧比的适应力,实现不同掺烧比时锅炉出力达设计值。根据分析,首先要确定合理的掺烧比设计点,其次要充分挖掘锅炉受热面的自适应能力。炉内受热面因掺烧废气烟温降低,辐射换热能力减弱时,尾部对流受热面因掺烧废气烟气量增大,对流换热能力提高,对炉内减少的吸热量进行弥补的能力。
结合项目需求反复核算和设计,本项目锅炉设计点按70%掺烧比设计,通过炉内、外受热面布置方式和布置面积的调整,实现了在纯燃煤和90%掺烧燃气之间,锅炉出力达到设计值的目的。0%、30%、60%、90%掺烧比时炉内外受热面的吸热量情况如图3所示。
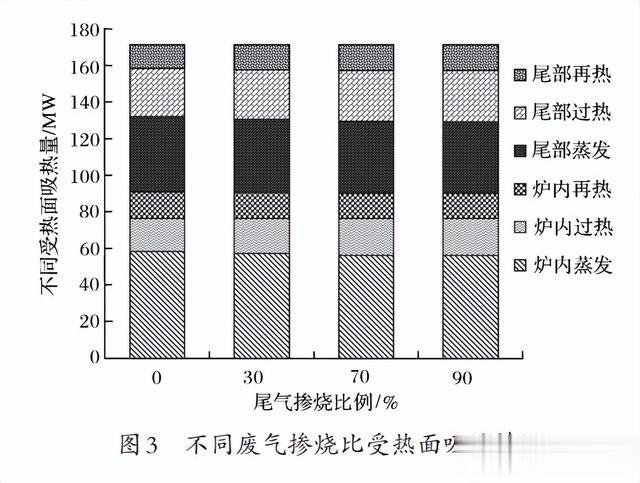
由图3可知,炉内外受热面在不同掺烧比时吸热量存在一定变化,但总吸热量都能维持在同一水平。
2.3 掺烧比-效率曲线
效率作为锅炉设备最重要的性能指标之一,代表设备设计制造水平及锅炉运行水平。对锅炉效率有影响众多因素中,燃料影响最大。因此有掺烧废气任务的机组,运行时如何选择合理的掺烧比,在处理废气的同时尽量提高锅炉效率是用户和运行人员最关心的问题。
根据分析,废气掺烧对锅炉效率的影响主要体现在q2(排烟损失)、q4(固体未完全燃烧)和q6(灰渣热损失):随着废气掺烧量增加,排烟量和排烟温度提高,q2增加;同时,因燃煤比例下降,灰渣量降低,飞灰、低渣含碳量基本不变的情况下,q4和q6下降。可见掺烧废气对q2与q4、q6的影响相反,因此锅炉效率与掺烧比的关系可能存在3种情况:①燃用热值高、灰分低、挥发分高的优质煤,q4和q6本身较小。随着掺烧废气量增加,降低绝对值小于q2增加值,锅炉效率随着掺烧废气的增加而下降。②燃用热值、挥发分低,灰分、水分高的差煤,q4和q6在损失中占比大。随着掺烧废气量增加,q4和q6下降的绝对值大于q2增加值,锅炉效率随掺烧废气的增加而升高。③燃用热值、灰分、挥发分中等的常规燃煤,随着掺烧废气量增加,q4和q6下降趋势与q2增加趋势相差较小,锅炉效率可能呈现多种变化,需具体计算分析。
本项目燃用煤质为矸石,初步计算下来纯燃矸石的锅炉效率不到89%;而燃用兰炭尾气的燃气炉,在同等环境条件下,计算效率大于90%。因此,初步分析本项目掺烧比-效率曲线为第二种情况。通过计算,在不考虑实际配风需求,仅按最经济的设计过量空气系数考虑,得到q2、q4、q6和锅炉效率如图4所示。由图4可知,q2增加趋势小于q4和q6下降之和,效率曲线随掺烧比例增加呈上升趋势,与第二种情况基本吻合。
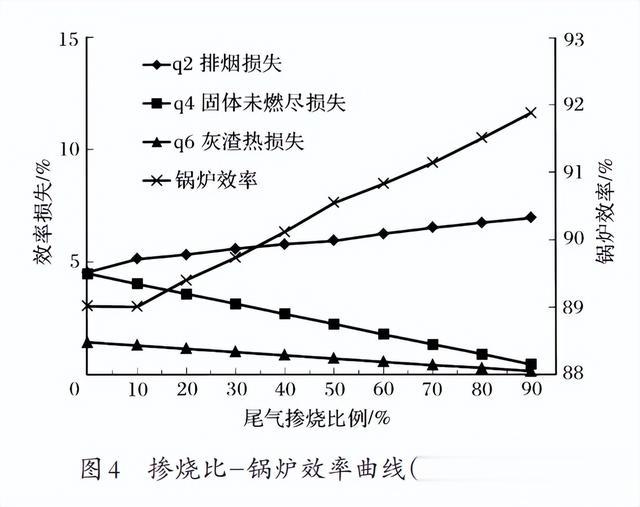
实际工程中,因保证流化状态、设备安全等需要,炉底流化风、回料风、播煤风、各管道冷却风均不得小于1个最小值。随着废气掺烧比例提高,燃气配风随之增加,但流化风等达到最小值后则不再降低,因此实际工程中会出现当掺烧比例达到一定值时,入炉空气总量超过设计过量空气系数,导致烟气量增加,锅炉效率会在一定范围内呈现下降趋势。经计算,在本项目条件下,70%掺烧比例时,流化风等达到最小值,掺烧比例进一步提高,过量空气系数将随之提高。80%掺烧比时过量空气系数较70%时增加0.2左右,q2损失增幅是设计过量空气系数条件下的3.6倍。70%到80%掺烧比之间的锅炉效率出现局部下降趋势,如图5所示。根据掺烧比-锅炉效率曲线的趋势,综合考虑燃烧稳定性、避免因床料添加带来电耗,可以得出70%废气掺烧比综合经济性较好。
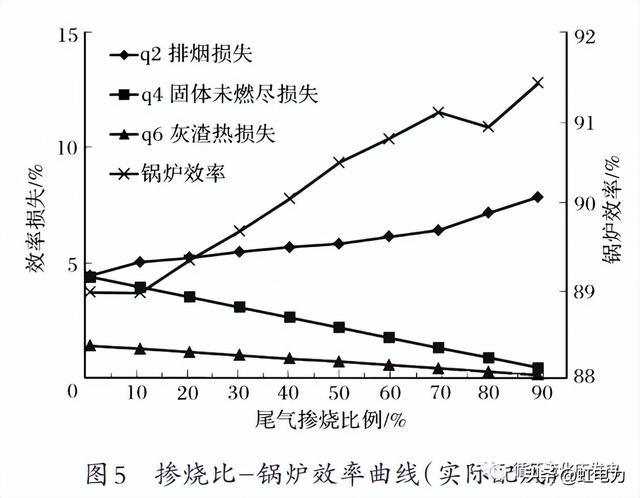
3 锅炉设计方案
基于以上技术和设计方案的运用,目前完成220t/h掺烧兰炭尾气超高温亚临界锅炉方案如图6所示。
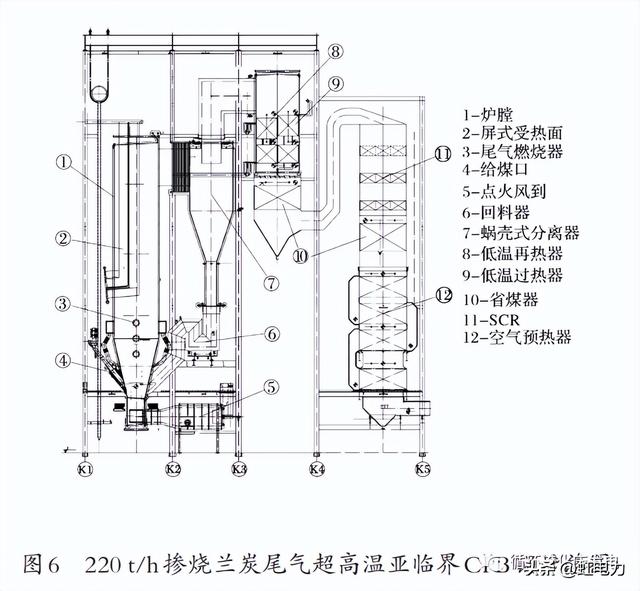
由图6可知,锅炉本体采用M型布置;第一跨为炉膛,炉内高过、中过和高再采用屏式布置;第二跨为冷却式旋风分离器,回料器采用非机械式;第三跨为尾部烟道,烟道上部采用汽冷包墙结构、双烟道设计,前后烟道分别布置蛇形管式低再、低过,烟道下部为绝热钢板结构,布置有高温省煤器,并设计有灰斗;考虑到90%掺烧兰炭尾气工况时,锅炉NOx原始排放接近燃气炉,仅采用SNCR脱硝无法满足环保要求,因此尾部设计三层SCR反应器,并拖出第四跨布置;SCR反应器下方为低温省煤器和管式空气预热器。
本项目采用双点火风道进风和小型柱状型风帽设计能够进一步保证炉内流场的均匀性;由于炉内受热面采用屏式布置,为避免兰炭尾气燃烧时火焰喷涂受热面,最上层燃烧器距离屏底留有足够距离;考虑到电厂经济性,减少厂用电率,本项目分离器采用高效蜗壳式设计,通过提高分离效率在较高掺烧比时保证炉内固体颗粒浓度和物料平衡,减少在线床料添加系统投入。
4 结语
采用循环流化床锅炉大比例掺烧处理可燃废气,首先要保障燃气和燃煤在炉内稳定燃烧;其次通过合理选取燃料设计点和调整受热面布置使锅炉有宽掺烧比达到设计出力的能力;最后掺烧废气对锅炉效率的影响会因煤、燃气情况不同而各异,通过针对分析得到相应掺烧比-效率曲线可以对运行有实际指导意义。文中以220t/h掺烧兰炭尾气项目为例进行方案设计,实现了0~90%废气掺烧比例。同等条件下,兰炭尾气掺烧比70%时炉内燃烧稳定性好、锅炉效率高,同时也满足了项目掺烧兰炭尾气的需求。
文献信息
[1]张强,杨虎,邓启刚,鲁佳易,苏虎,黄敏,邱彬彬,徐磊.大比例掺烧低热值废气循环流化床锅炉设计[J].节能,2021,40(01):66-69.