前言
2023年3月3日,埃安发布全新一代高性能集成电驱技术“夸克电驱”,2024年8月23日,夸克电驱2.0在锐湃动力科技公司量产下线,以非晶合金量产为核心突破,驱动电机最高效率98.5%,最高转速30000rpm,功率密度13kW/kg。非晶合金作为一种新型软磁材料,一次又一次得到了更多关注。
01#
常用软磁材料分类和应用
软磁材料是电力电子、信息电子等产业的基础材料之一,具有磁电转换的特殊功能,广泛应用于电能变换、抗电磁干扰、无线充电、近场通讯等领域,在新能源汽车、新能源发电、消费电子、工业电子、通讯、云端服务、计算机以及航空航天等行业有着大量应用。
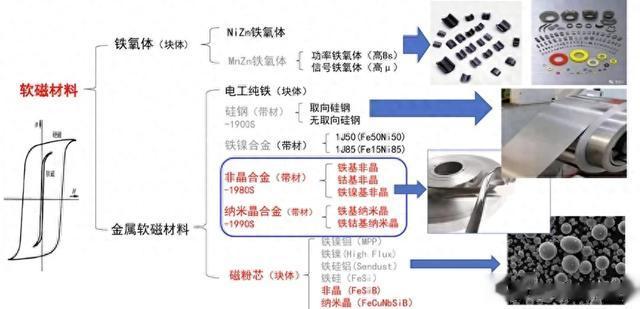
图1 常用软磁材料
软磁铁氧体仍为当前规模最大的软磁材料,是以Fe2O3为主成分的亚铁磁性氧化物,根据配方差异可分为锰锌、镍锌等多种类别。性能上可分为功率软磁铁氧体材料(用于能量转换/模电范围)和高磁导率软磁铁氧体材料(用于电磁兼容、信号传输/数电范围)。
硅钢片按生产工艺分为热轧硅钢和冷轧硅钢,冷轧硅钢分为冷轧无取向硅钢和冷轧取向硅钢,是制造发电机、电动机和变压器铁芯的主要材料。
金属合金软磁粉是指含有铁、硅及其他多种金属或非金属元素的粉末,包括铁硅磁粉、铁硅铝合金磁粉和铁硅铬磁粉、铁镍磁粉等。金属合金软磁粉可进一步加工为磁芯,主要用于制作功率电感元件。
非晶合金种类主要包含铁基、铁镍基、钴基非晶合金。纳米晶超薄带具有高饱和磁度、低矫顽力、高初始磁导、高居里温度率等优势,综合软磁性能优于铁氧体,可缩小磁性器件体积、降低磁性器件损耗、提高效率,可用于共模电感、电子变压器等领域。
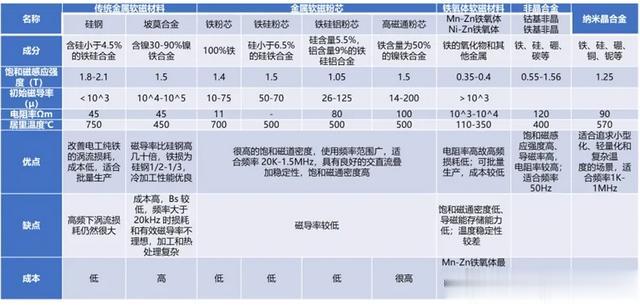
表1 常用软磁材料对比
02#
常用磁性器件分类和应用
磁性器件是以法拉第电磁感应定律为原理,由磁芯、导线、基座等组件构成,实现电能和磁能相互转换的电子元器件,是属于电子元器件行业领域的重要分支。主要包括电子变压器、电感器等。
变压器是利用电磁感应来实现交流电压升降或阻抗变换功能的电子元件,由铁芯(或磁芯)和线圈组成。
电感器可以将电能以磁性的形式存储的被动电子元件,是电子电路中的基础无源元件之一,分为传统插装式电感器及片式电感器。非晶合金在配电变压器、电抗器(高频)等已成功应用,纳米晶合金在高频变压器、电流互感器、共模电感等已成功应用,非晶和纳米晶在电机上的应用仍在探索之中。
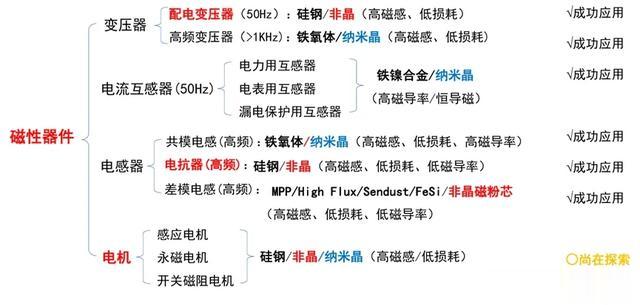
图2 常用磁性器件
软磁材料和器件除了在传统部件如整车控制器VCU、车身 EMI、低频天线、组合仪表、抬头显示器、智能内后视镜、电子时钟、显示屏,以及一些控制器、传感器、摄像头等应用之外,在直流充电桩、车载充电机OBC、车载DC/DC变换器、高压配电盒PDU、驱动电机系统等新能源汽车新增部件大量应用。

图3 软磁材料和器件在新能源汽车新增部件大量应用
新能源汽车集成了大量软磁器件,例如EMI滤波器中的共模和差模电感,PFC电路中的PFC电感,DC/DC电路中的谐振电感、高频变压器、DC滤波电感等,正在向高频化和大功率方向发展。
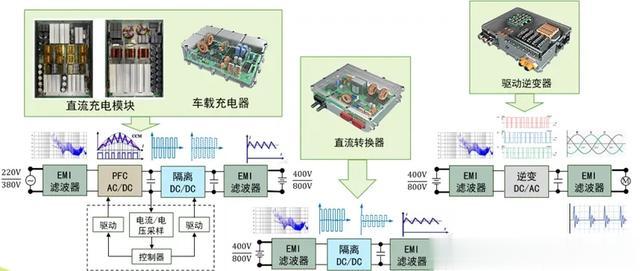
图4 软磁材料和器件在新能源汽车高压电路大量应用
03#
非晶软磁合金发展历程和市场情况
从1960年美国Duwez教授发明用快淬工艺制备非晶态合金开始,非晶软磁合金的发展大体上经历了两个阶段:
第一个阶段到1988年,1984年美国四个变压器厂家在IEEE会议上展示实用非晶配电变压器则标志着第一阶段达到高潮,1989年美国Allied Signal公司已经具有年产2.5万吨非晶带材的生产能力,全世界约有100万台非晶配电变压器投入运行,所用铁基非晶带材几乎全部来源于该公司。
从1988年开始,非晶态材料发展进入第二阶段,标志性事件是日本日立金属公司的Yashiwa等人在非晶合金基础上通过晶化处理开发出纳米晶软磁合金(Finemet),当年日立金属公司纳米晶合金实现了产业化。
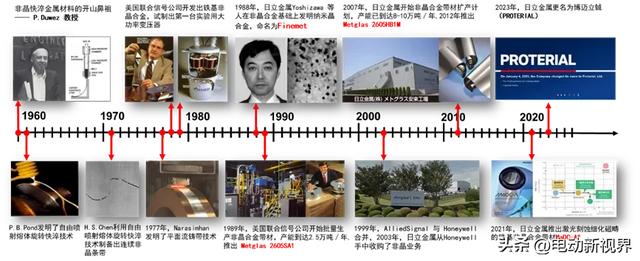
图5 国外非晶软磁合金发展历程
国内非晶材料研究始于1975年,国家科委从“六五”开始连续5个五年计划均将非晶、纳米晶合金研究开发和产业化列入重大科技攻关项目。其中标志性的成果分别是:“七五”期间建成百吨级非晶带材中试生产线,带材宽度达到100mm;“八五”期间突破了非晶带材在线自动卷取技术,并建成年产20万只非晶铁心中试生产线;“九五”期间,成立了国家非晶微晶合金工程技术研究中心,建成了千吨级非晶带材生产线,带材宽度达到220mm,同时建成年产600t非晶配电变压器铁心生产线。通过前4个五年科技攻关计划的实施,我国基本实现了非晶合金带材及制品产业化。根据 2021年中国钢铁工业协会和金属学会“冶金科学技术奖评选结果”,国内由安泰科技、青岛云路等 6 家单位共同完成的“宽幅超薄铁基纳米晶带材工程化技术开发及应用”项目已取得成功,新开发的超薄纳米晶带材连续化生产装备及制造工艺,填补了国内技术空白。
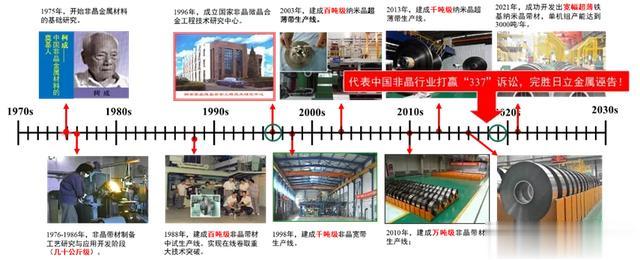
图6 国内非晶软磁合金发展历程(钢铁研究总院—中国钢研集团—安泰科技)
国内外非晶带材的产量在2015年达到一个高峰,2016年后国产非晶带材产量激增;随后,随着电网用配电变压器招标数量降低,非晶带材连续几年减量;2021年下半年开始,由于取向硅钢价格上涨、立体卷变压器的推广,非晶带材的需求逐渐回暖,市场拉动产量逐渐恢复,未来增长趋势还在继续。目前日立金属在全球处于领先地位,国内主要企业包括安泰科技、云路股份、中研非晶、兆晶科技、江苏国能、河南中岳等。
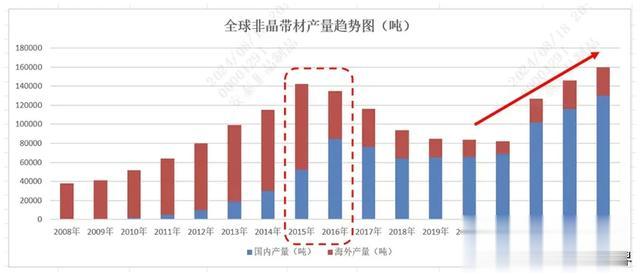
图7 全球非晶带材产量
04#
非晶软磁合金材料特性、制备工艺和应用情况
非晶合金又称“液态金属或金属玻璃”,其主要制品非晶合金薄带是采用急速冷却技术将合金熔液以每秒百万度的速度快速冷却,得到厚度约0.03mm的非晶合金薄带,其物理状态表现为金属原子呈长程无序的非晶体排列。得益于上述极端生产工艺形成的特殊原子结构,使得非晶合金相较于传统材料硅钢具有低矫顽力、高磁导率、高电阻率等良好的性能。

图8 非晶合金材料特性
除了非晶带材,目前非晶合金还有粉末、丝材、块体、涂层等其他产品形态。

图9 非晶合金产品形态
非晶带材平面流铸工艺采用急冷凝固技术,就是将母合金融化后,通过喷嘴包喷射在一个高速旋转的冷却辊上,瞬间冷却形成像纸一样薄薄的带子。有几个特点:
▶ 冷却速度快:液态合金的温度基本在1400-1500℃,瞬间凝固到接近室温,冷却速度达到了每秒百万度的级别;
▶ 喷带速度快:30m/s好比一颗子弹刚刚飞出去的速度,而要把接近子弹速度的物体抓住是非常困难的;
▶ 厚度薄:喷出带材的厚度20-30μm,精度控制主要通过喷嘴包下面的狭缝及辊嘴间距的设计来实现。
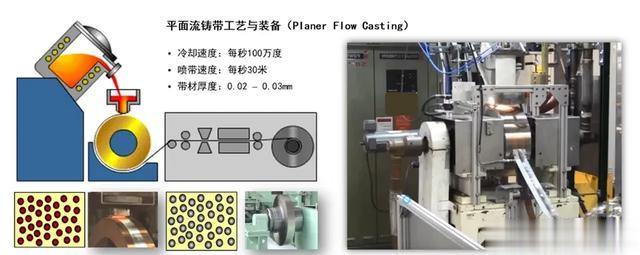
图10 平面流铸工艺与装备
非晶合金种类主要包含铁基、铁镍基、钴基非晶合金。铁基非晶合金广泛应用于节能配电变压器;铁镍基非晶合金应用范围与镍坡莫合金对应,但其在能量损耗和机械强度方面更加优越,应用于漏电开关、磁屏蔽等,钴基非晶合金在非晶合金中具有最高的磁导率,且具有优异的耐磨性和耐蚀性,应用于要求严格的军工电源中的变压器、电感等,可替代坡莫合金、铁氧体等。铁基非晶材料典型应用场景如下图所示。

图11 铁基非晶材料典型应用场景
05#
铁基非合金在驱动电机上的应用
定转子铁心材料是决定驱动电机性能的关键,目前量产的驱动电机基本采用高牌号无取向硅钢进行功率能量转化。我国无取向硅钢主要以低牌号为主,未来新能源车驱动电机、大型电机以及节能电机趋势下,高牌号无取向硅钢需求有望持续增长。我国从大批量使用0.35mm材料逐步转为0.27-0.30mm产品,个别批量使用0.20mm和0.25mm产品。
高性能铁心材料有多种技术路线,包括:6.5%Si高硅钢(又名超级硅钢)、钴铁合金、镍铁合金、非晶材料等。在1kHz,1T条件下,铁基非晶单位损耗仅为传统硅钢的1/10,非晶定子电机的铁耗较硅钢电机降低50%-70%以上,适应于新能源汽车主驱电机的高频高速高效化发展趋势。目前,非晶材料饱和磁感低于无取向硅钢,非晶电机峰值转矩和电机体积较硅钢电机仍有差距,电机设计和材料性能需进一步提升优化。另外,非晶定子加工技术仍是产业化技术瓶颈,多层非晶带材复合粘接技术、针对超薄超硬材料的冲压技术有望突破。
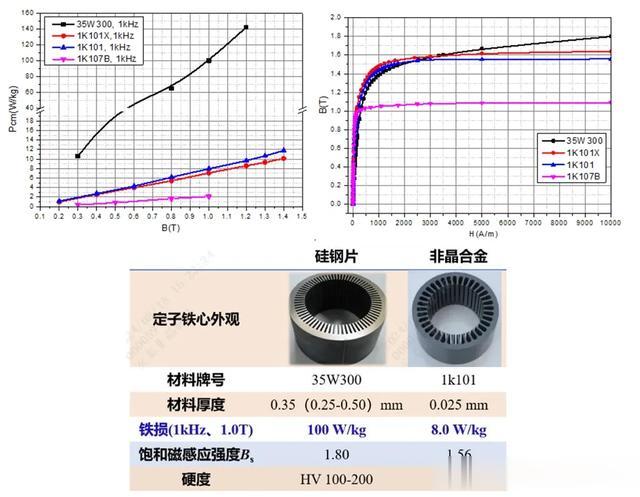
图12 非晶合金和硅钢片性能对比
根据夸克电驱发布数据,其采用非晶合金饱和磁感1.65T,铁芯铁损P1.0/400达到5.7W/kg,带材宽度232mm。定子量产冲压节拍180次/min,量产模具寿命10万台,量产一致性合格率93%。
来源:电动汽车产业技术创新战略联盟,RIO电驱动